Building Statistics
General Building Data
Building Name: US Lacrosse Headquarters & Training Center
Building Site: 2 Loveton Circle, Sparks, MD 21152
Building Occupant: US Lacrosse Center, LLC / MedStar Sports Medicine
Height: 38’-0”
Number of Stories: 2 above grade, 1 below grade
Dates of Construction: April 2015 – May 2016
Project Cost: Approximately $11.6 million
Project Delivery Method: GMP converted to a lump sum
Project Team
Architecture
Design and Function:
The US Lacrosse Headquarters & Training Center is a 45,000 square foot, three-story facility located in Sparks, Maryland, 20 miles north of Baltimore City. This facility accommodates office and conference space, video production, and a US Lacrosse museum located on the upper two floors of the building. On the lower floor below grade, two separate locker rooms and a referee room occupy the east side of the building. Also on the lower floor, a Medstar Sports Medicine is located on the west and south sides adding training and rehabilitation functions to this facility. Finally, one of the major focal points aesthetically and functionally is a 98,000 square foot turf lacrosse field located on the east side is designed for both the men’s and women’s game with bleachers and a tunnel attached to the locker rooms. Between this field and the building is a large portico that runs down the full length of the building leading to a path around the field connecting the sport to the building itself.
Sustainability:
USL has a variety of sustainable features included in its design. An UltraPly TPO Roofing System is installed which will help the building’s cooling requirements due to its reflective features. Open Offices are located adjacent to the long spans of windows so the maximum amount of natural light can reach these open spaces. The turf field will be made out of 100% recyclable turf, therefore making the green even greener.
Building Size

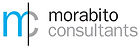






Owner
US Lacrosse
Center, LLC
Owner's Rep.
HDC Project Management
General Contractor
Gilbane Building Company
Architect
Rubeling
& Associates
Structural Engineer
Morabito Consultants, Inc.
Civil Engineer
Matis
Warfield, Inc.
MEP Engineer
Kibart Consulting Engineers
Landscape Architect
Site
Resources, Inc.

Figure 1: A view of the east side of the building highlighting the curved balcony and tapered roof.
Applicable Codes:
US Lacrosse Headquarters and Training Center was designed, at minimum, to the following codes:
-
2012 International Building Code
-
2012 State of Maryland Fire Prevention Code
-
2012 International Mechanical Code
-
2012 National Standard Plumbing Code
-
NFPA 70 National Electrical Code
-
NFPA 72 National Fire Alarm Code
-
Title 9 of the Environment Article, Annotated Code of Maryland
Zoning:
The Baltimore County authorities designate the local area of the project to be Business Type II B. With the local zoning ordinances the building is restricted to a maximum height of 3 stories or 55’-0” high and a maximum floor area of 23,000 SF per floor. There are no historical requirements for this project.
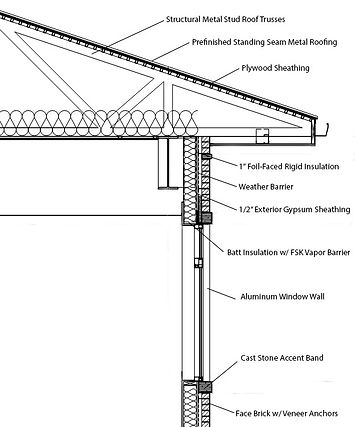
Building Envelope:
The building enclosure consists of brick veneer walls detailed with cast stone accent bands and split up by aluminum window walls. The front entrance on the west side includes an exterior insulation and finishing system (EIFS) canopy and curved wall. The back entrance on the east side of the first floor consists of a larger EIFS curved wall as well as an aluminum storefront system encompassing the glass doors. Above this entrance on the second floor is an EIFS balcony attached to a curved aluminum storefront which connects it to the building. This balcony is surrounded by a glass railing system and is supported by aluminum panel clad columns (See Figure 1). This east side entrance leads out to a large portico that’s runs along the entire length of the building at the top of the bleachers.
Roofing:
The roofing is made up of tapered, aluminum roof panels as well as a fully adhered thermoplastic polyolefin (TPO) membrane system where it is flat on top. These formed metal panels are both flat seamed and standing seam (See Figure 2). The roof maintains the same slope of 4:12 around the entire building but adds a convex curved shape above the balcony on the east side. Flashing on this roof includes valley flashing at the curve, hip flashing at the corners and rolled drip-edge flashing at the flat seamed section.
Figure 2: Wall section through the second floor east exterior wall
Part 1: Project Background
Part 2: Engineering Systems
Primary Engineering Systems
Construction:
For this project it was decided a Hambro decking system would be installed (see Figure 3). This is of major constructability concern because it needs to be installed correct to ensure the correct strength after forming and curing of the concrete. Also, the temporary joists used in this system must be installed to correctly account for deflection of the floor slabs. Safety is also a major piece of installing a Hambro system since workers must go underneath the slab and remove everything holding it up and trust that it has cured into a structurally sound piece of the building. To accommodate this risk, the concrete contractor brought in a Hambro system specialist who has successfully installed decks in this manner.

Figure 3: Detail of the Hambro floor system being installed courtesy of www.swirnowstructures.com
Another unique feature of the building that must be planned for is that the slab on grade drops at the south end making it two different elevations. Foundation wall construction had to be carefully planned since these walls have different heights due to the split of lower and upper S.O.G. Also, before pouring the S.O.G. a knee wall separating the slab had to be installed, waterproofed and backfilled to maintain the proper grade throughout the building.
Contract Information:
The contract for this project is interesting because it is hard to give it an exact title. This project has elements of a Lump Sum contract and also a Guaranteed Maximum Price contract. It is a Lump Sum contract in the fact that U.S. Lacrosse accepted the estimated amount Gilbane proposed the project would cost and will pay Gilbane that amount at the end of the job. Any money not used on the job Gilbane will retain. Where the GMP side of the contract comes into play is the fact that there is an Owner’s contingency included. This means an amount of money is included in case of issues on the job that the general contractor may use so it doesn’t exceed the contract amount. If there is any money left over it goes to the Owner.
Electrical:
Power to the US Lacrosse HQ will be provided by a 277/480V, 3 phase, 4 wire main distribution panel at 1200A. This MDP panel supplies three transformers which feed power and lighting to each floor separately. The ground floor transformer is of size 45 KVA while the first and second floor require transformers of size 75 KVA. This system steps down from 277/480V to 120/208V at the lighting distribution panels for each floor.
Lighting:
Office lighting fixtures will be 2x2 and 2x4 recessed LED fixtures. Waiting areas and conference rooms will use 6” recessed LED downlights as well as 8’ suspended LED fixtures above conference tables. Larger hallways such as the elevator lobbies will be provided with 277V recessed high output LED slot fixtures. Lastly, the museum space requires a line voltage light track to create the needed effect in that area.
Lighting control will be provided by a distributed occupant sensing control system, which will communicate through wireless gateway when an occupant enters a room and requires low voltage wiring. In open offices and lobbies these sensors will be organized into zones based on usage. In the private offices, manual on/off local switches will be provided but will also have automatic off capabilities if the room is left unattended long enough.
Mechanical:
Two Variable Air Volume rooftop units will service the entire US Lacrosse Headquarters. These rooftop units are direct expansion cooling gas heating systems and will be located in the North and South ends of the rooftop mechanical space. RTU-1 will service the North end of the first and second floors as well as the entire ground floor while RTU-2 will service the south end of these floors. These VAV rooftop units will then split into two separate types of VAV systems. The first system is a Parallel Fan powered Variable Air Volume box which supplies the larger areas around the exterior such as the open offices and museum space. The second system is a Single Duct VAV box with heating water reheat that supplies the more centralize spaces like the individual offices and bathrooms as well as help supply the larger areas.
A ductless split system Air Handling Unit located on the roof will be employed to keep the server room cool. Also, 8 exhaust fans located throughout the mechanical rooms, electrical rooms, locker rooms and toilet rooms will be installed to control the air quality in these spaces.
Structural:
The structural system for the US Lacrosse Headquarters and training facility consists of a concrete foundation that supports a structural steel system with concrete floor slabs and a truss roof. The foundation employs 24 spread footers with a typical size of 9.5’ x 9.5’ x 25” (l x w x h) with 10#6 vertical reinforcing but can get as large as 11’ x 11’ x 28” with 10#7 reinforcing and as small as 8’ x 8’ x 21” with 10#5 reinforcing. At the Ground Floor, 16 out of the 24 footers support concrete pedestals at 24” x 24” with 8#9 vertical reinforcing. The other 8 footers located inside the building footprint support steel columns of sizes W10x68 and W10x60. The foundation walls are 16” thick and 15’-8” below grade surrounding the lower S.O.G. and 12” thick and 12’-8” below grade surrounding the higher S.O.G. A 3’ tall and 8” thick knee wall runs through the building west to east tying together the upper and lower slab, completing the substructure (see Figure 4).


The superstructure for this building is made up of steel columns, beams and joists. Column sizes range from W10x33 to W10x68 with the W10x68’s being the most common. Floor Heights are 14’ and 12’ for the first and second floor above grade and 12’-8” and 15’-8” for the ground floor below grade. Steel beams have three spans along east to west direction. The exterior spans are 40’ long and have beam sizes of W24x76 and W30x99. The interior span of 21’-4” consists of beam sizes W12x53, W12x58 and W12x65 moving from the middle outward. Steel beams running in the north south direction have 5 spans that average 28’. Towards the middle beam sizes are W21x44 and W18x40 as the beams move outwards. Concrete floor slabs are built using a Hambro system; therefore, a metal deck isn’t required underneath the concrete. Lateral resistance is provided by two stairways that run up through the entire middle of the building on the North and South Central locations.
Figure 4: A view of the substructure from the lower slab on grade
Figure 5: A look at the substructure, superstructure and truss design for the roof of the US Lacrosse Headquarters
Truss design will create the tapered roof system using a metal deck on metal studs to support the roofing materials (see Figure 5). A cut out in the center of the roof will house the rooftop mechanical units and will rest on a flat roof built like the concrete floor slabs underneath.
Engineering Support Systems
Fire Protection:
US Lacrosse Headquarters will have a fire suppression system with 319 sprinklers and a flow rate of 2631 GPM for the entire building. The ground floor will be a tree type system and the first and second floors will be a wet type system. At the tunnel under the portico, a dry pipe system will be installed to avoid pipe freezing. A fire hydrant was installed on site that makes one connection to the city water main on the adjacent street. Spray fireproofing will be applied to the first floor framing and its supporting columns.
Transportation:
Elevators
US Lacrosse Headquarters will have one elevator, centrally located in the building that will service all 3 floors. The elevator is sized at a standard 3,500 lb capacity and requires a dedicated 125 volt 20 ampere single-phase power supply. Admittance to the second floor from this elevator will require card access.
Stairs
Two main stairwells are located inside the building at the central core and the north end. Both stairwells access every floor of the building but a card reader is required for admittance to the second floor. Two smaller stair cases are placed in this building due to the 3 foot slab height difference between upper S.O.G. and lower S.O.G. These are located at the south end and allow access to the MedStar training and rehabilitation space. One of these staircases also includes an adjacent handicap lift to allow disabled occupants to move throughout MedStar.
Telecommunications:
The telecommunication system is provided through four, 4” conduits. Verizon Fios is the main communication service to the building but an extra conduit was added to house Comcast Service for redundancy. Both Comcast and Verizon have fiber and standard service available. A Closed Circuit Television security system and card access system will be included in the telecommunication service. This will help decrease public access to private parts of the building and keep US Lacrosse employees safe. IP telephones will be installed in the building. Lastly, Extra conduit was also added for the planned future expansion of the building.